Steve Smart - of Smart Opals - shares how he got his start supplying the Opal Jewelry Trade
Traveling to the Tucson Gem Show this year was a little different than in years past. We opted to bypass some of the bigger venues in exchange for smaller and more intimate experiences. And it turned out to be one of our best trips yet. Among the unforgettable memories made, was a private interview with Steve Smart, Owner of and Cutter for Smart Opals. Hailing from the Sunshine Coast of Australia, Steve has been cutting Australian Opal for 18 years and is a true master of his craft. Join us as we ask him about his journey into opal cutting.
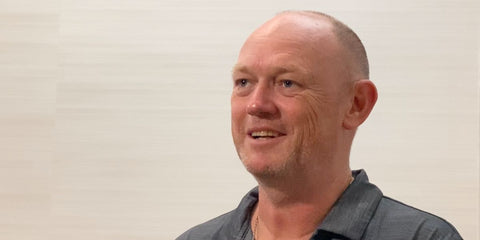
Steve Smart of Smart Opals
THE SETUP:
Upon their arrival in Tucson for the 2024 Tucson Gem Show, we met Steve and Evelyn Smart at their hotel. Their room had a remarkable setup for gem vendors. With a long, narrow desk, maybe 10-12 feet long, it was an ideal setup for displaying and examining their range of Boulder, Crystal and Black Opals.
After a warm reunion, introductions (to my friend Lisa Kim of Lisa Kim Fine Jewelry ) - and imbibition of just enough champagne for a toast, we dove into our interview.
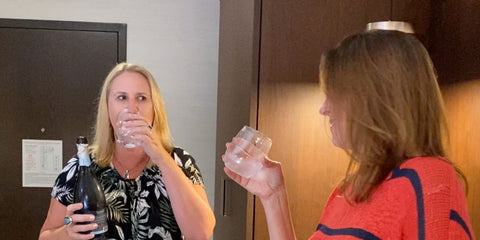
Reuniting with a toast with Evelyn Smart
THE INTERVIEW:
1. I wanted to talk to you a little bit about how you got started in the opal cutting business, and I was hoping you could tell us a little more about your operation.
Answer: Yeah, sure. So I started off as a pilot and out of Sydney and these guys that had Opal mines had a plane and one day their regular pilot couldn't do the flight, so they were hunting ‘round for the right guy that could fly that plane. And I had that endorsement. So off we went. And so I flew them to Sydney to a little town called Quilpe, and that's in Western Queensland. And then from there, they gave me the choice to stay in town and just hang out or come out to the mine and get involved.

Quilpie and Sydney, Australia
So out I went and yeah, we rocked up there at the mine site and there was this huge boulder that was in the way of where they were trying to dig. So they drilled it all out and packed it with dynamite and ran the lead out. And as soon as I arrived on site, they're like, ah, you can do the shot. So yeah, <laugh> bang, and that was it. I was hooked. It was good fun. So I was out there with a sledgehammer next to the excavator and they had a little tunnel that we were doing and yeah, I just got involved helping with that.
2. Did you have any primary mentor along the way?
Answer: Yeah, well the guy that had the mine, it was two brothers, Walter Huber. So through the years, yeah, we've become good friends. But when I sort of left the flying, the airline job that I had a few years later and I wanted to actually learn how to cut, I rang him up and just asked if he had some opal I could buy just to start learning on. And yeah, I ended up buying two 44 gallon drums of rough opal as my first parcel, and I had no idea how to cut it, <laugh>.
And so we did a deal where he'd show me how to cut the opal and we'd share in the proceeds from that. And yeah, we basically spent a year cutting that one parcel together.
3. Do you remember the very first opal that you cut?
Answer: Well, <laugh>, the first opal I would've cut, would've been with a brick saw. You know, we're digging out these boulders from this mine, and they're like, you know about this big <gestures to encompass a space about 1.5-2 feet in diameter>, most of them. And it's just slicing these things up with a brick saw, so you can see the veins of opal inside the rock. And then back then we were working from this little house in Quilpie and they were doing some preliminary cutting out there and actually had a sandblaster set up, which I thought was a pretty cool way too, to do some cutting and it was just trialing it. So I was on the sandblaster and yeah, we were just getting pieces of boulder opal that had been partially faced up and I was just there blasting the last of the ironstone off the face to get the clean face.
So yeah, we did hundreds and hundreds of pieces just with a sandblaster. It's not one particular stone, but a series of stones. Yeah. Look, I don't remember the first stone I cut from start to finish because he taught me basically from the polishing stage back. Right.
So the polishing stage, you can sort of, you can teach anyone to do it. It's just, you know, that stone that felt or leather buff with this polish, you know, and just make sure you get the whole stone and then you go back through the next stage sanding. Okay. So then I learned that, and then back into the coarser grits and then the diamond grinding and the preforming of the stone. Then into the small, the six inch saw work that we do to uncover the veins of opal in boulder. And then, you know, right back to, yeah, just chopping it up with the brick saw.
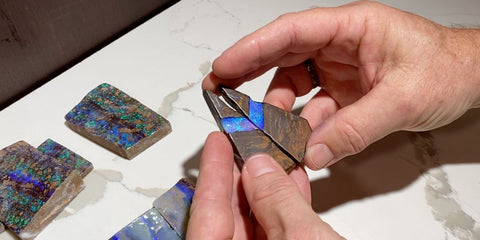
Examples of some larger opal splits
4. So what do you think is the hardest part of cutting an opal and what is your favorite part?
Answer: Of cutting? Yeah, they're the same process, the six inch trim saw. So when you have a boulder like this with a vein of opal through it, you need to get like a big saw just to break it down into a section you can handle on the smaller saw. Okay. So, you know, your first cut is usually just like through the middle or slicing it into chunks that's done with a brick saw. And then you get it down to something that's about the size of your fist that you can use with a trim saw, like a six inch blade like this.
And that's where you can really start to be precise with your cutting and say, okay, well there's a vein of opal there and a vein of opal there. I'm gonna cut down through the middle. Or you can say, you know, there's a vein of opal there and I'm gonna try and split it so you can use the saw to start that little process and then click it open with a blade so that that process of breaking down the Boulder Opal from a chunk of rock into faced up material where you can see the color, a lot of that is done on the six inch saw.
And that's where the money is made or lost really, because all the processes that follow after that are working from what you've uncovered. And if you don't get that part of the process right, you're, you're chopping through opal that you can't ever get back.
5. What about when you're picking rough; can you give us any tips?...for you, what is it really that you're looking for or looking to avoid? What do you get excited about when you see it in rough?
Answer: Yeah, look, I mean, you know, big thick veins of red is great, but it's just so hard to find like, you know, I haven't seen a parcel like that ever really, you know, you just, you just can't find it. So when you see something that has a bit of red through it, obviously that's the most valuable and most sought after color. You know, if there's red in there, you buy it just because that's red in your stock.
Right. But just for, you know, generally what's available, the blue greens are good. You're looking for veins that, you know, have a bit of thickness to them if possible. The process that I use, I'm actually carving and I can get down to very, very fine veins of opal and I can still get a stone out with the process that I have. So, okay.
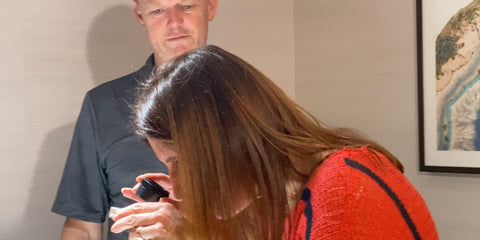
Steve showing Nicki some opal inclusions under the loupe
You know, I can, yeah, I can handle thinner veins, but you know, you're just making sure that the material is gonna be stable.
Steve showing Nicki some opal inclusions to check under the loupe
You know, if you see lots of cracks going down across the veins of opal, you know that when you open it up it's just gonna be full of cracks. Right. So you're trying to avoid that and [you want] nice, solid, stable material and yeah, just see what comes out.
6. Yeah. What about your favorite stone you've ever cut?
Answer: Favorite stone? Well, you know, they're all pretty special for different reasons, but yeah, I mean, the one I wear around my <laugh> around my neck, that's gotta be.
(Nicki: You have to tell us that story now, <laugh>...I love this story.)
Yeah, well, so that first parcel, the two 44s [two 44 gallons of rough opal], you know, we're chopping through it. And Walter's father, Ted, was helping us cut, and he would've been mid eighties at the time, and he's just on the saw just working away day after day. And I just found this rock in amongst all the stuff that had been faced up and it was basically just that. And so, yeah, I really thought it was cool.
It's a nice sort of masculine looking stone. I thought, ah, Ted will love this. So I gave it to him and, you know, he is very grateful and, you know, I never saw it again. Ted passed away unfortunately, so I don't know where that stone is. But about a decade after I gave Ted that stone, I bought another parcel of rough off the same miners. And it was just, it was a funny parcel. It was little bits and pieces in buckets and a bit of a mix. And I've got it home and I'm going through it and I find this piece and yeah, it really, it's very distinct.
Yeah. So I knew what it was straight away, when an opal cleaves and there's two faces of opal, the first face is what I gave to Ted, and yeah, I found the second one a decade later. So yeah, my daughter made the pendant and that's what I wear. Yeah. I love that one.
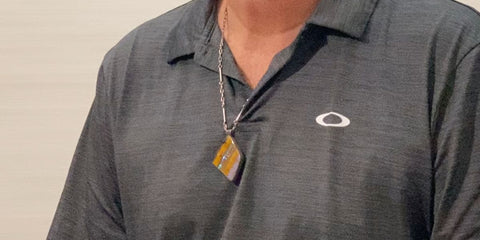
Steve’s favorite Opal - the second face of the opal split
7. So Steve, I wanted to ask you, when it comes to sourcing rough - without crossing any proprietary boundaries - can you tell us a little bit about where you get your material?
Answer: Yeah. Well, I mean, the first parcel of material I ever bought was from the Stelzer family. They have a mine called the IC Mine, and they're a family business. You know, there's a couple of generations there working together and they've been mining that hill for like 30 or 40 years or something. So that's where I buy as much as I can from, you know, so, and then other material I try and source, you know, from people that you sort of meet along the way and you get a good feeling about them and you know you can trust them and yeah, they've got great materials.
So, yeah, it's a good relationship. I've tried to build up these relationships over a long period of time because when good material comes out, you know, there's probably a few people they can call to say there's a parcel, come and have a look. So you sort of want them to call you first, if possible. So sourcing material is a bit tricky, and I think I always try and pay the maximum that I think I can afford to pay for a parcel, because it's gotta work for everyone.
You know, the guy paying for the diesel to dig it out has to make money as well. So I try and look at a parcel and work out what it's worth in my environment when I’ve finished it. And then, yeah, pay appropriately for the rough.
8. And for those customers that are buying that are concerned about ethical purchases and the hands that these gemstones pass through - when it comes to Australian Opals (obviously it depends who you're buying from) … if buying your [Smart Opal] stones, is it fair to say it goes from miner to cutter to…designer?
Answer: Yeah, totally. I'm buying rough material from miners…and I try and get out to their mines, you know, to see the way they're working. And so, yeah, I buy off the miner, I cut it myself, and then, you know, I'm selling to people that are making the end product. So there's not much of a way to shorten that route. You know…that's about the minimum hands it can go through because although a lot of miners like to cut, they don't actually have all the tools and all the skills to really make the most of all of the material that they've got.
So yeah, this sort of needs to be those people in their own little specific area doing their job well for it to work nicely.
9. And to take the ethics a step further, when it comes to the land that the mines are on - even though that's not your primary focus - can you speak to us at all about how Australia governs mining the lands?
Answer: Yeah, it's, it's a very complicated process, to be honest. Like, to get a mining lease in Queensland where the Boulder Opal comes from, it can take years because the mines department has quite a strict sort of criteria and a process, and that involves the native title parties in that area. So the aboriginal groups that have established themselves there long before we turned up with machines, they get a say in how the process occurs.
So, yeah, it's fair to say that there's pretty strict controls over how the mining's done, so, yeah. And when you're working with good people, you know it's, yeah, it's being done ethically and environmentally friendly - if that's a thing when you're burning a bit of diesel. But yeah, I try and work with good people in that respect.
10. Steve, thank you so much for sitting down with us today. I appreciate it. So if anybody watching would like to find you, where is the best place or the best places to find you?
Answer: Well, we're on Instagram of course. Just trying to keep in touch with the day to day of what we're doing. So @smartopals. And we also have a website with stock on it, smartopals.com.au and cut material from Lightning Ridge and from Queensland. So we're just trying to have a good range of stock up there from, you know, $20 stones up to, you know, as good as we can get out of the rough. So there should be something there for everyone.
POST INTERVIEW:
While the interview was a lot of fun, and I loved learning more about Steve in that context, my favorite part of the evening was actually after the interview formalities. Steve and Evelyn graciously invited us to stay; we took them up on their offer during which we dined, discussed life, and of course, perused their opals.
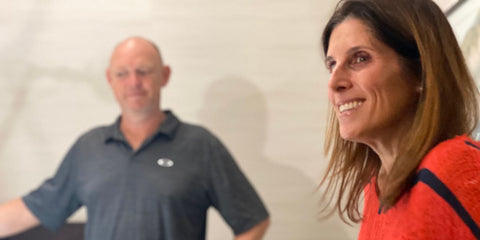
Steve and Nicki (of NIXIN Jewelry)
Favorite Takeaways:
- It was during this subsequent exchange that I learned about Steve’s passion to cultivate precise and safe cutting techniques in the opal cutting community. I know a few of the individuals he has already helped to support, and was impressed by the interest he expressed in advancing his profession, not only for himself, but for others as well.
- I learned that Steve pays close attention to customer feedback, and folds it into his business as appropriate. He shared with us how an experience with one prominent designer with strict criteria for opal selection altered his cutting process. After his encounter with them, he began louping every opal in his inventory before offering it for sale. He holds himself accountable to the highest standards.
- According to Steve, working with artists, true creatives, is a top priority to him. As a designer who creates one of a kind opal jewelry, that’s a concept I both respect and appreciate.
- Just like Steve said he tries to “work with good people,” I feel strongly about doing the same. And Steve and Evelyn Smart are just that - good people.
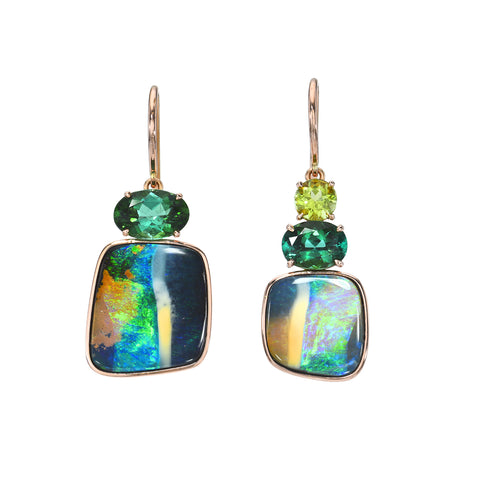
Twilight Shores Australian Opal Earrings by NIXIN Jewelry - Opals cut by Steve Smart
Come Explore the magic of Australian Opals.